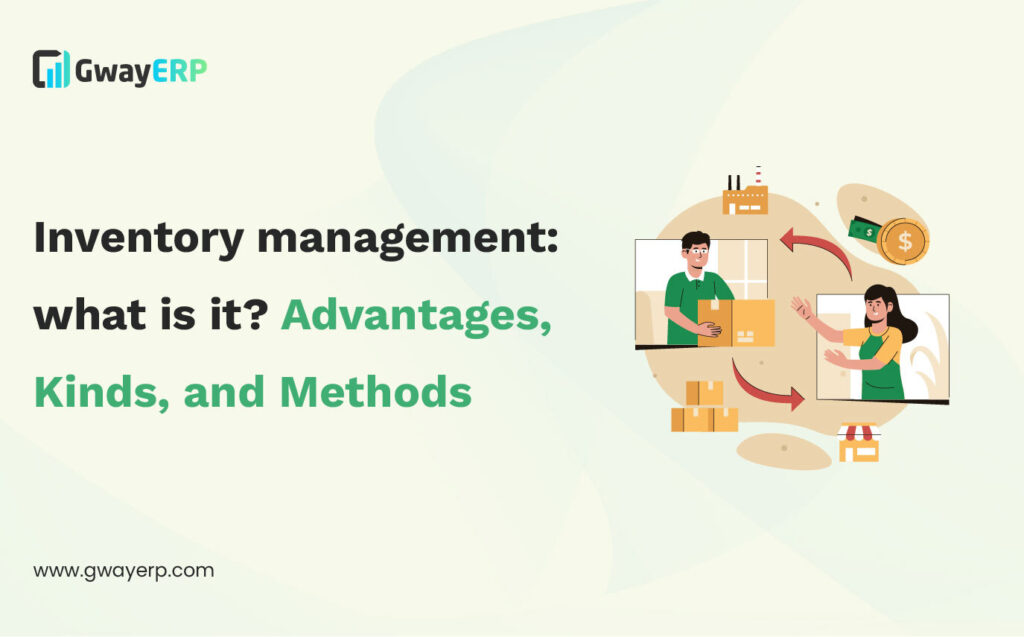
Introduction:
In the dynamic landscape of modern commerce, the meticulous handling of inventory stands as a linchpin for organizational success. Efficient inventory management isn’t merely a logistical necessity; it’s the strategic backbone that determines profitability, customer satisfaction, and operational fluidity. This comprehensive guide navigates through the intricacies of inventory management, offering insights into its advantages, diverse methodologies, best practices, and the evolving trends shaping its future.
From warehouses stacked with products to streamlined supply chains catering to global demands, this guide delves into the crux of inventory management. It explores the pivotal role played by optimized stock control, forecasting techniques, and adaptive strategies in aligning supply with demand. With each section meticulously crafted to offer practical knowledge, real-world examples, and proactive solutions, this guide aims to equip businesses—big or small—with the tools necessary to revolutionize their inventory management practices.
Join us on this enlightening journey as we unravel the nuances of inventory management, from understanding its advantages to embracing cutting-edge technologies and forecasting the future trends that will redefine the landscape of inventory control. Whether you’re an industry veteran seeking to fine-tune your methods or a newcomer eager to grasp the fundamentals, this guide is designed to illuminate the path toward achieving operational excellence through effective inventory management strategies.
A. Definition of Inventory Management:
Inventory management refers to the systematic control and overseeing of a company’s stock of goods, raw materials, work-in-progress items, and finished products. It involves the strategic planning, organizing, and monitoring of inventory levels to ensure optimal stock availability, minimize carrying costs, prevent stock outs, and meet customer demands efficiently. This process includes various facets like inventory tracking, demand forecasting, procurement, storage, and logistics management to maintain a delicate balance between supply and demand.
B. Importance in modern business operations:
In the contemporary business landscape, effective inventory management stands as a cornerstone of operational success. Its significance lies in its ability to streamline processes, enhance cash flow, and drive profitability. By maintaining accurate inventory levels, businesses can respond promptly to customer demands, minimize excess inventory costs, avoid stockouts that could lead to revenue loss, and optimize resources. Moreover, it fosters customer satisfaction through timely order fulfillment, nurtures stronger supplier relationships, and forms the backbone for data-driven decision-making across the supply chain.
C. Overview of what the blog will cover:
This comprehensive blog serves as a guiding compass through the intricate realm of inventory management. It encompasses a wide spectrum of essential topics, including the advantages of effective inventory management, different types and methods employed in the field, best practices for streamlined operations, real-life case studies exemplifying successful implementations, challenges faced, and futuristic trends shaping the industry. From exploring the benefits to providing practical insights, solutions, and forecasting the evolving landscape, this blog aims to equip businesses with actionable knowledge to revolutionize their inventory management practices.
Table of Contents:
I. Advantages of Effective Inventory Management
II. Types of Inventory Management
III. Methods and Strategies of Inventory Management
IV. Best Practices for Effective Inventory Management
V. Case Studies or Examples
VI. Challenges and Solutions in Inventory Management
VII. Future Trends in Inventory Management
VIII. Conclusion
I. Advantages of Effective Inventory Management:
Effective inventory management brings a myriad of benefits to businesses, including optimized cash flow, reduced carrying costs, improved customer satisfaction through timely order fulfillment, minimized stock outs, and enhanced operational efficiency. It facilitates better decision-making by providing accurate insights into stock levels and demand patterns.
A. Cost Reduction and Financial Efficiency:
Effective inventory management serves as a cornerstone for cost reduction and financial efficiency within businesses. By minimizing excess inventory and streamlining procurement processes, organizations can significantly decrease carrying costs associated with storing surplus goods. Furthermore, optimized inventory levels facilitate better cash flow management, freeing up capital that would otherwise remain tied up in overstocked items. This reduction in holding costs, coupled with strategic purchasing practices and efficient inventory turnover, directly contributes to improved financial health and profitability.
B. Improved Customer Satisfaction:
A well-managed inventory directly impacts customer satisfaction by ensuring products are consistently available when demanded. Maintaining optimal stock levels prevents stockouts, meeting customers’ expectations for timely deliveries and reducing the likelihood of lost sales due to unavailability. Additionally, accurate inventory management allows for better order accuracy, minimizing errors in shipment and improving overall customer experience. Satisfied customers foster loyalty, positive reviews, and increased referrals, all of which contribute to sustained business growth.
C. Optimized Production and Operations:
Inventory management plays a pivotal role in optimizing production and operational efficiency. By accurately forecasting demand and maintaining appropriate stock levels, businesses can align production schedules more effectively, reducing idle time and maximizing output. Additionally, efficient inventory practices streamline workflows, reducing bottlenecks in operations and enhancing overall productivity. This synchronization between inventory levels and production capacity helps minimize waste, improve resource utilization, and ultimately boosts operational effectiveness.
D. Minimized Risk of Stockouts and Overstocking:
One of the primary goals of inventory management is to strike a balance between avoiding stockouts and preventing overstock situations. Maintaining optimal inventory levels through accurate demand forecasting and inventory control measures minimizes the risk of stockouts, ensuring that customers’ needs are consistently met. Simultaneously, it mitigates the financial risks associated with overstocking, such as obsolescence, storage costs, and potential markdowns to move excess inventory. This equilibrium not only safeguards against lost sales but also prevents unnecessary tie-up of capital in surplus stock.
E. Enhanced Decision-Making through Data Insights:
Data-driven insights derived from effective inventory management systems empower businesses to make informed decisions. Through detailed analytics and reports, organizations gain visibility into demand patterns, supplier performance, and inventory turnover ratios. This data aids in identifying trends, optimizing stock levels, and adjusting procurement strategies in real-time. Armed with these insights, businesses can make proactive decisions, anticipate market changes, and adapt swiftly to evolving customer preferences, ensuring sustained growth and competitiveness in the market.
II. Types of Inventory Management:
Inventory management encompasses various approaches, including Just-in-Time (JIT), ABC analysis, Economic Order Quantity (EOQ), and Vendor-Managed Inventory (VMI). Each type caters to different organizational needs and focuses on streamlining inventory levels, procurement, and distribution processes.
A. Raw Materials Inventory:
Raw materials inventory comprises the foundational elements used in the production process. It encompasses the essential components and resources necessary for manufacturing goods. Managing this inventory effectively involves maintaining optimal stock levels, ensuring a steady supply of materials, and mitigating the risk of stockouts that could halt production.
B. Work-in-Progress Inventory:
Work-in-progress inventory encapsulates products in various stages of completion within the production process. It represents the transitional phase between raw materials and finished goods. Managing this inventory involves tracking the flow of goods through production stages, minimizing bottlenecks, and optimizing workflows to ensure efficient throughput.
C. Finished Goods Inventory:
Finished goods inventory consists of products that have completed the manufacturing process and are ready for sale or distribution. Effective management of finished goods inventory revolves around balancing supply with demand, preventing overstock situations, and ensuring timely delivery to meet customer needs without incurring excessive holding costs.
D. Maintenance, Repair, and Operations (MRO) Inventory:
MRO inventory comprises essential supplies and equipment necessary to maintain operational functionality. It includes items like spare parts, tools, and consumables crucial for equipment upkeep and facility maintenance. Managing MRO inventory involves strategic planning to avoid downtime, ensuring the availability of critical components, and optimizing inventory levels to reduce unnecessary expenses.
E. Consignment Inventory:
Consignment inventory is stock that remains the property of the supplier until the buyer utilizes or sells the goods. This arrangement allows businesses to store inventory without immediate ownership, minimizing holding costs. Managing consignment inventory involves maintaining accurate records, monitoring usage, and negotiating favorable terms with suppliers to optimize the arrangement.
F. Just-in-Time (JIT) Inventory:
JIT inventory is a strategy focused on receiving goods only as they are needed in the production process, minimizing excess inventory and storage costs. This approach aims to synchronize production with customer demand, reducing waste, and enhancing efficiency through precise inventory control and close supplier relationships.
G. ABC Analysis (Activity-Based Costing):
ABC analysis categorizes inventory items based on their significance in terms of cost and usage. It classifies items into categories (A for high-value items, B for moderate, and C for low-value items) to prioritize management attention. Implementing ABC analysis involves segmenting inventory, allocating resources based on item importance, and optimizing inventory control strategies tailored to each category’s requirements.
III. Methods and Strategies of Inventory Management:
Multiple methods and strategies exist within inventory management, such as demand forecasting, safety stock optimization, inventory turnover ratio analysis, and software-based inventory control systems. These approaches aid in maintaining an optimal balance between supply and demand while minimizing excess or shortage issues.
A. Economic Order Quantity (EOQ):
Economic Order Quantity (EOQ) is a fundamental principle in inventory management that aims to strike the optimal balance between ordering and holding costs. By calculating the ideal quantity to order, considering factors like demand variability and ordering costs, businesses can minimize inventory holding expenses while ensuring sufficient stock levels to meet customer demands. EOQ offers a mathematical framework that helps organizations determine the most cost-effective order quantities, thereby optimizing inventory management practices and streamlining procurement processes.
B. Just-in-Time (JIT) and Lean Inventory Systems:
Just-in-Time (JIT) and Lean Inventory Systems operate on the premise of minimizing waste and maintaining lean inventory levels. JIT emphasizes a synchronized production system that delivers components or goods precisely when needed, reducing excess inventory and associated holding costs. Lean inventory systems, inspired by JIT principles, focus on continuous improvement, waste reduction, and efficient resource utilization. These systems enhance operational efficiency, responsiveness, and cost-effectiveness by synchronizing supply with immediate demand, fostering agility in production and distribution.
C. Vendor-Managed Inventory (VMI):
Vendor-Managed Inventory (VMI) is a collaborative supply chain model where the supplier manages the customer’s inventory levels. In this arrangement, suppliers monitor stock levels and replenish inventory autonomously, based on predefined agreements or real-time data sharing. VMI fosters closer relationships between suppliers and buyers, ensuring optimized stock levels, reduced stockouts, and minimized holding costs for the customer. It streamlines the replenishment process, allowing for a more efficient and cost-effective supply chain operation.
D. Drop shipping and Cross-Docking:
Drop shipping and Cross-Docking are logistics strategies that streamline inventory management and order fulfillment. Drop shipping involves fulfilling customer orders directly from suppliers without storing inventory, reducing the need for warehousing space and inventory holding costs. Cross-docking, on the other hand, involves transferring incoming goods directly from inbound to outbound transportation, minimizing storage time and handling costs. Both strategies focus on efficiency by reducing inventory handling, storage, and associated costs while improving order fulfillment speed.
E. RFID and Barcode Technology Integration:
The integration of RFID (Radio-Frequency Identification) and barcode technology revolutionizes inventory management by providing real-time visibility and accurate tracking of inventory movements. RFID tags and barcodes enable businesses to monitor inventory throughout the supply chain, from manufacturing to distribution and retail. RFID’s ability to transmit data wirelessly and barcode’s ease of use streamline inventory tracking, reduce errors, and enhance inventory accuracy, enabling better decision-making and improving operational efficiency.
F. Software and Automation in Inventory Management:
Software and automation play pivotal roles in modern inventory management systems. Inventory management software offers functionalities for inventory tracking, demand forecasting, order management, and stock optimization. Automation tools streamline routine tasks like order processing, inventory replenishment, and data entry, reducing human error and enhancing operational efficiency. The integration of software and automation empowers businesses to manage inventory more effectively, improve accuracy, and respond swiftly to dynamic market demands.
IV. Best Practices for Effective Inventory Management:

Adopting best practices like regular inventory audits, setting reorder points, implementing automation where applicable, fostering strong supplier relationships, and utilizing data analytics to forecast demand ensures a well-organized and efficient inventory management system.
A. Accurate Demand Forecasting:
Accurate demand forecasting serves as the bedrock of effective inventory management. By analyzing historical data, market trends, and consumer behavior, businesses can anticipate future demand patterns with greater precision. Leveraging sophisticated forecasting models and tools, such as time-series analysis or machine learning algorithms, empowers organizations to make informed decisions regarding stock levels, production schedules, and procurement strategies. This proactive approach minimizes the risk of overstocking or stockouts, ensuring that inventory aligns closely with actual customer needs, thus optimizing operational efficiency and maintaining a competitive edge in the market.
B. Regular Inventory Audits and Cycle Counts:
Conducting regular inventory audits and cycle counts is instrumental in maintaining the accuracy of stock records. These systematic checks involve physically verifying on-hand inventory against recorded data, identifying discrepancies, and rectifying inaccuracies promptly. By implementing a consistent audit schedule, businesses can mitigate the risk of inventory shrinkage, reduce errors in stock levels, and uncover operational inefficiencies. This meticulous approach not only ensures that the inventory remains aligned with recorded figures but also instills confidence in decision-making processes, fostering a more robust and reliable inventory management system.
C. Efficient Supply Chain Collaboration:
Efficient supply chain collaboration stands as a cornerstone of effective inventory management. Establishing strong partnerships and transparent communication channels with suppliers, distributors, and logistics partners streamlines the flow of goods, reduces lead times, and minimizes disruptions. Collaborative initiatives, such as Vendor-Managed Inventory (VMI) or joint forecasting efforts, facilitate a synchronized supply chain ecosystem. By sharing information and coordinating efforts across the supply chain, businesses can optimize inventory levels, respond swiftly to market changes, and enhance overall operational agility.
D. Implementing Inventory Optimization Tools:
The implementation of inventory optimization tools and software solutions revolutionizes inventory management practices. These tools leverage advanced algorithms to analyze data, determine optimal stock levels, and automate replenishment processes. Whether it’s through Material Requirements Planning (MRP) systems, RFID technology, or cloud-based inventory management software, businesses gain real-time visibility into their inventory, enabling smarter decision-making. These tools not only streamline inventory control but also provide actionable insights, empowering organizations to adjust strategies proactively and adapt to evolving market dynamics.
E. Training and Empowering Staff:
Training and empowering staff are critical elements in ensuring the success of inventory management initiatives. Equipping employees with comprehensive training programs on inventory procedures, data management tools, and best practices cultivates a knowledgeable workforce capable of executing tasks with precision. Empowering staff by fostering a culture of ownership and accountability instills a sense of responsibility in maintaining accurate inventory records and efficient processes. Well-trained and empowered employees contribute significantly to the success of inventory management efforts, driving operational excellence and continuous improvement within the organization.
V. Case Studies or Examples:
Examining case studies or real-world examples can elucidate successful inventory management implementations. For instance, analyzing how a particular company improved its inventory turnover ratio or how a retail giant mitigated stockouts through strategic inventory planning provides valuable insights.
A. Successful implementation stories showcasing improved business outcomes:
Case studies abound with compelling narratives of businesses that have orchestrated remarkable turnarounds through astute inventory management. Consider the tale of Company X, a manufacturing conglomerate that struggled with bloated inventory and erratic supply chains. By adopting a Just-in-Time (JIT) approach coupled with robust demand forecasting models, they drastically reduced excess stock while ensuring timely production schedules. This streamlined operation led to a 30% reduction in carrying costs and a noteworthy 20% boost in customer satisfaction due to timely deliveries.
Another remarkable example is Retailer Y, which battled persistent stockouts affecting their bottom line. Through the implementation of sophisticated inventory tracking systems and smarter reorder strategies, they managed to reduce stockouts by 50%. This optimization not only improved revenue but also bolstered their reputation, transforming them into a preferred shopping destination due to their consistently stocked shelves.
B. How different industries leverage various inventory management methods:
Across industries, inventory management methods are tailored to meet specific demands and challenges. In the automotive sector, the adoption of Vendor-Managed Inventory (VMI) ensures a seamless supply of components, allowing manufacturers to minimize warehouse space and reduce costs while maintaining production continuity. Contrasting, the retail sector thrives on ABC analysis, categorizing products based on their importance to optimize inventory levels—high-demand items receive tighter inventory control, while lower-demand items are managed with more flexibility.
The healthcare industry heavily relies on Just-in-Time inventory to minimize waste and ensure critical supplies are readily available without overstocking. Meanwhile, the food and beverage industry employs FIFO (First In, First Out) methods to manage perishable items efficiently, reducing the risk of spoilage and ensuring product freshness. Such diverse approaches underscore the adaptability of inventory management strategies, tailored to suit the unique demands of different sectors.
VI. Challenges and Solutions in Inventory Management:
Inventory management faces challenges such as demand variability, stock obsolescence, inaccurate forecasting, and supply chain disruptions. Solutions involve leveraging technology for accurate demand forecasting, employing agile inventory strategies, and implementing risk mitigation plans.
A. Inventory Obsolescence and Expiry:
Inventory obsolescence and expiry represent critical challenges within the realm of inventory management. Storing goods for extended periods can lead to products becoming obsolete or reaching their expiration dates, resulting in financial losses and operational inefficiencies. Managing this issue involves vigilant monitoring of inventory levels, implementing robust FIFO (First In, First Out) or FEFO (First Expired, First Out) systems, and establishing clear protocols for the disposal or liquidation of obsolete stock. By actively addressing expiration risks and regularly reviewing inventory, businesses can minimize the impact of obsolescence, optimize shelf life, and maintain a healthier bottom line.
B. Seasonal Demand Fluctuations:
Seasonal demand fluctuations present both opportunities and challenges for inventory management. Industries experience peaks and troughs in consumer demand based on seasons, holidays, or trends. Balancing inventory levels to meet increased demand without overstocking requires astute forecasting, agile production planning, and strategic marketing efforts. Leveraging historical data, market trends, and predictive analytics enables businesses to adapt inventory levels accordingly, ensuring adequate stock during peak seasons while mitigating excess inventory risks during slower periods.
C. Supply Chain Disruptions and Risks:
Supply chain disruptions pose substantial threats to inventory management, disrupting the flow of goods and impacting inventory availability. External factors like natural disasters, geopolitical instability, or supplier issues can severely affect supply chains. To mitigate these risks, businesses need contingency plans, diversified sourcing strategies, and close collaborations with suppliers. Implementing agile supply chain practices, maintaining buffer stock, and employing technologies such as blockchain for transparent supply tracking can fortify against disruptions, ensuring a more resilient and responsive supply chain.
D. Technology Integration and Upkeep:
Technology integration is pivotal in modern inventory management, offering tools and systems that streamline processes and enhance efficiency. However, ensuring the seamless integration and upkeep of technology poses its own challenges. Regular system updates, training employees on new software, and safeguarding against cybersecurity threats are essential tasks. Embracing advanced inventory management software, IoT devices for real-time tracking, and AI-driven analytics not only optimizes operations but also demands continuous monitoring and investment in technological upgrades to stay ahead in the competitive landscape.
VII. Future Trends in Inventory Management:
The future of inventory management is poised for advancements in technology, including the use of AI-driven predictive analytics, blockchain for transparent supply chains, IoT-enabled tracking for real-time inventory visibility, and sustainability-focused inventory practices.
A. AI and Machine Learning Integration:
AI and machine learning have revolutionized inventory management by providing sophisticated tools to analyze vast amounts of data swiftly and accurately. Through pattern recognition and predictive algorithms, these technologies forecast demand, identify trends, and optimize inventory levels in real-time. AI-driven systems not only enhance forecasting accuracy but also enable automated decision-making, reducing human error and enhancing operational efficiency. By leveraging AI and machine learning integration, businesses can adapt swiftly to market changes, streamline inventory processes, and ultimately improve overall supply chain performance.
B. Blockchain in Supply Chain Management:
Blockchain technology has emerged as a game-changer in supply chain management, offering transparency, security, and traceability across the entire supply chain. Its decentralized ledger system ensures an immutable record of transactions, enhancing trust among stakeholders and minimizing fraudulent activities. In inventory management, blockchain enables end-to-end visibility by tracking each product’s journey from manufacturer to consumer. This technology not only mitigates counterfeiting and enhances product authenticity but also streamlines inventory tracking and simplifies reconciliation processes between different entities within the supply chain.
C. Sustainability and Green Inventory Practices:
The paradigm shift toward sustainability has prompted the integration of eco-friendly practices into inventory management. Green inventory practices aim to reduce waste, minimize carbon footprints, and optimize resources throughout the supply chain. From adopting recyclable packaging materials to implementing energy-efficient transportation and storage methods, businesses are increasingly focusing on sustainable inventory management. Such practices not only align with corporate social responsibility initiatives but also resonate with environmentally conscious consumers, fostering brand loyalty and long-term viability.
D. Predictive Analytics for Inventory Optimization:
Predictive analytics has become a cornerstone of inventory optimization, empowering businesses to make data-driven decisions proactively. By analyzing historical data, market trends, and customer behavior, predictive analytics forecasts future demand patterns with remarkable accuracy. These insights enable companies to fine-tune their inventory levels, minimize excess stock, and anticipate fluctuations in demand, thereby reducing holding costs and stockouts. The integration of predictive analytics fosters a responsive and agile inventory management system, ensuring a competitive edge in today’s fast-paced markets.
VIII. Conclusion:
In conclusion, effective inventory management plays a pivotal role in the success of businesses, optimizing resources, reducing costs, and enhancing customer satisfaction. Embracing innovative strategies and staying abreast of evolving trends is crucial for sustained efficiency in inventory management.
A. Recap of key points:
Throughout this comprehensive exploration of inventory management, several critical aspects have surfaced. We’ve highlighted the advantages of efficient inventory control, showcasing its impact on cash flow optimization, customer satisfaction, and operational efficiency. We’ve elucidated the various types, methods, and strategies, underscoring the importance of tailored approaches in meeting diverse business needs. Additionally, best practices and case studies have illuminated actionable insights, emphasizing the necessity of proactive and data-driven decision-making. Understanding challenges and solutions while peering into future trends completes this holistic view, providing a roadmap for businesses aiming to thrive through effective inventory management.
B. Emphasize the significance of inventory management in modern businesses:
In today’s competitive landscape, the significance of inventory management cannot be overstated. It serves as the cornerstone of efficient operations, wielding the power to influence a business’s bottom line and customer satisfaction levels. The ability to maintain optimal inventory levels, forecast demand accurately, and navigate supply chain complexities is pivotal. Effective inventory management not only streamlines internal processes but also fosters resilience in the face of market fluctuations and consumer demands. It stands as an indispensable pillar upon which modern businesses build their success, enabling agility, cost-effectiveness, and sustained growth.
C. Encouragement for continuous improvement and adaptation to new methodologies:
In the realm of inventory management, the only constant is change. The landscape continuously evolves, driven by technological advancements, shifting consumer behaviors, and global market dynamics. Embracing a mindset of continuous improvement and adaptation to new methodologies is not just advantageous—it’s imperative. Businesses must remain agile, willing to integrate innovative technologies, refine existing processes, and adopt emerging strategies to stay ahead. The journey towards excellence in inventory management demands a commitment to learning, evolving, and leveraging new methodologies to drive efficiency, responsiveness, and competitive advantage.